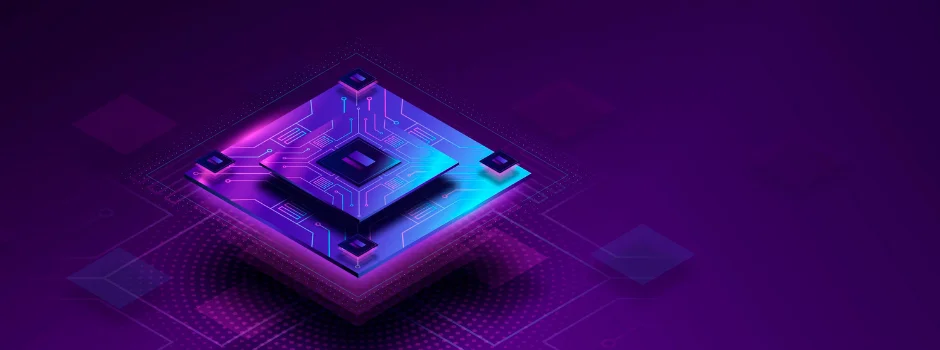
Top 8 Critical Challenges Faced by VLSI Designers in 2025
Mar 13, 2025 7 Min Read 120 Views
(Last Updated)
The design cycle time faces a startling reality – verification bottlenecks eat up more than 70% of it. This eye-opening statistic expresses just one of the many challenges VLSI designers face in today’s semiconductor industry.
Today’s chips pack billions of transistors, which makes design complexity a huge obstacle to overcome. The shift to smaller technology nodes like 5nm and 3nm creates new challenges, especially when you have to manage power consumption and handle manufacturing variations.
This detailed guide will help you find the eight most important challenges VLSI designers must tackle in 2025. We’ll explore everything from power management problems in portable devices to time-to-market pressures that affect design quality. You’ll gain valuable insights into what these challenges mean for the semiconductor industry.
Table of contents
- What do VLSI Designers Do?
- Top 8 Challenges Faced by VLSI Designers
- 1) Increasing Design Complexity
- Ways to Overcome:
- 2) Power Management Issues
- Ways to Overcome:
- 3) Signal Integrity and Timing Closure
- Ways to Overcome:
- 4) Debugging and Verification Challenges
- Ways to Overcome:
- 5) Electromagnetic Interference (EMI) and Electromagnetic Compatibility (EMC) Issues
- Ways to Overcome:
- 6) Manufacturability and Yield Optimization
- Ways to Overcome:
- 7) Cost and Time-to-Market Pressures
- Ways to Overcome:
- 8) Interdisciplinary Skills Requirement
- Ways to Overcome:
- Takeaways…
- FAQs
- Q1. What are the main challenges faced by VLSI designers in 2025?
- Q2. How does power management impact VLSI design?
- Q3. What role does verification play in VLSI design?
- Q4. How do manufacturing challenges affect VLSI design?
- Q5. What skills are essential for VLSI designers in 2025?
What do VLSI Designers Do?
VLSI designers are the brains behind microchips and integrated circuits that power everything from smartphones to autonomous vehicles. Their work includes multiple specialized areas. Each area needs unique expertise and technical skills.
These professionals have the complex job of fitting thousands, sometimes millions, of transistors onto a single chip. They carefully engineer integrated circuits through several key stages. The process starts when they understand what’s needed and turn those needs into logical blueprints.
VLSI designers use specialized Computer-Aided Design (CAD) tools to place and connect millions of transistors, capacitors, and resistors on silicon substrates. They focus on making three things better: speed, power consumption, and area utilization.
VLSI designers combine their knowledge of digital and analog circuitry with expertise in specialized tools and methods. Their work helps advance semiconductor technology and makes them essential in today’s fast-changing world of electronic innovation.
Top 8 Challenges Faced by VLSI Designers
The semiconductor industry faces unprecedented challenges because chip designs are becoming more intricate. VLSI designers must overcome many obstacles to create reliable integrated circuits. These obstacles range from managing power consumption to ensuring signal integrity.
Modern VLSI design requires knowledge in multiple domains. Designers must be skilled at various tools and techniques while keeping up with technology that changes faster. The need for diverse expertise creates a steep learning curve and requires ongoing professional development.
Let’s discuss these challenges and some ways to overcome or avoid them:
1) Increasing Design Complexity
Today’s VLSI designs have reached mind-boggling levels of complexity. Circuits now pack millions of gates and intricate interconnections that need precise planning. The move to smaller node sizes, particularly 3nm technology, has made chip design far more complex.
Designers face tough challenges when they work with multiple logic layers. They need to blend various IP blocks from different sources while ensuring everything works together smoothly. The number of connections needed has shot up as more modules fit onto a single chip.
Smaller component sizes create a big headache. The rules for design have become incredibly detailed – just look at the 32nm process. It needs thousands of rules spread across about a thousand pages. These strict requirements make it harder to finish routing and meet market deadlines.
Ways to Overcome:
- Hierarchical Design Approach: Implement modular and hierarchical design techniques to manage complexity efficiently.
- AI & ML in Design Automation: Use AI-driven Electronic Design Automation (EDA) tools for optimized layout, verification, and debugging.
- Design Reuse & IP Integration: Utilize pre-verified intellectual property (IP) blocks to reduce development time and design risks.
- Advanced Verification Techniques: Employ formal verification, hardware emulation, and digital twins to validate designs early.
- Collaborative Design Workflows: Leverage cloud-based design platforms to enhance collaboration and parallel development.
2) Power Management Issues
VLSI design faces a major power consumption challenge. Mobile platforms dedicate almost 50% of their space just to power conversion circuits. Advanced technology brings tighter voltage requirements, making it harder for designers to manage power efficiently.
Circuits leak power even when they’re idle through transistor leakage currents. Advanced process nodes make this problem worse. The leakage gets high even when transistors are off. Static power now takes up a big chunk of total power consumption and affects battery life and running costs.
Dynamic power creates another major challenge with two key parts. The first part involves power that transistors use during active switching. The second part deals with short-circuit power that gets wasted when PMOS and NMOS transistors conduct at the same time. These elements directly affect how devices perform and how long their batteries last.
Poor power management does more than just drain batteries. Data centers spend 60-70% of their operating costs on power. This big expense shows why power optimization matters not just for mobile devices but also for large computing systems.
Ways to Overcome:
- Low-Power Design Techniques: Implement clock gating, power gating, and dynamic voltage and frequency scaling (DVFS) to minimize power usage.
- Advanced Transistor Technologies: Use FinFETs, Gate-All-Around (GAA) FETs, and other low-leakage transistor architectures to reduce power leakage.
- Efficient Power Delivery Networks (PDNs): Optimize PDN design with decoupling capacitors and advanced power grid architectures to improve power integrity.
- AI-Driven Power Optimization: Leverage AI/ML algorithms for dynamic power management and predictive analysis in chip design.
- Thermal-Aware Design: Integrate advanced cooling solutions, such as 3D stacking with efficient heat dissipation techniques, to manage power-related thermal challenges.
3) Signal Integrity and Timing Closure
Signal integrity and timing closure are leading VLSI design challenges today. Research suggests that one in five chips fails because of signal integrity problems. These failures cost companies heavily through photomask expenses, engineering resources, and delayed product launches.
Circuits keep shrinking as Moore’s law continues. Wires now sit closer together because of increased interconnect density, which creates more crosstalk between neighboring nets. Advanced nodes show higher sidewall capacitance compared to ground capacitance, and this raises induced noise voltage levels.
The timing closure process will give a reliable way to verify that all circuit paths meet their timing requirements. This vital phase affects how well the final chip works, how efficient it is, and how reliable it becomes. Industry data shows we need to test timing at twenty or more corners to guarantee proper closure.
These issues become critical as power density rises in smaller chips. Hot spots concentrate in specific areas and can damage the chip or make it wear out faster if not handled properly.
Ways to Overcome:
- Enhanced Power Distribution Networks (PDN): Optimize PDN design to minimize IR drop and maintain stable voltage levels across the chip.
- Crosstalk Mitigation Techniques: Implement shielding, proper spacing, and differential signaling to reduce noise and interference.
- Advanced Timing Analysis Tools: Use static timing analysis (STA) and sign-off tools with AI-driven optimizations to achieve faster timing closure.
- Clock Tree Optimization: Employ techniques like clock gating, skew balancing, and multi-corner multi-mode (MCMM) analysis for better timing convergence.
- Design-for-Manufacturing (DFM) Techniques: Consider process variations early in design using predictive modeling and margin-aware optimization.
4) Debugging and Verification Challenges
VLSI design faces major bottlenecks in debugging and verification. These processes take up about 60% of the total formal verification time. Modern chips have become so complex that functional debugging has become one of the biggest hurdles in the design cycle. Bugs have grown larger and more widespread.
Static timing analysis helps validate timing requirements throughout the design. Engineers break down the design into time paths and analyze timing details. The verification process needs multiple iterations to ensure everything works as designs become more complex.
Design and testbench synchronization creates unique problems.
Teams need to re-verify extensively when they modify designs, fix bugs, or upgrade testbenches. Even with strict configuration management and version control systems in place, perfect synchronization remains a constant challenge.
Ways to Overcome:
- Adopt AI-Driven Verification – Leverage machine learning to automate test case generation, detect anomalies, and accelerate debugging.
- Shift-Left Testing Approach – Integrate verification early in the design cycle to catch errors before synthesis and layout.
- Emulation and FPGA Prototyping – Use hardware-assisted verification to test real-world performance efficiently.
- Hybrid Verification Strategies – Combine simulation, formal verification, and emulation to enhance coverage and accuracy.
- Cloud-Based Verification – Utilize scalable cloud computing resources to handle large-scale verification workloads.
If you want to kickstart your career in VLSI Design, then GUVI’s VLSI Design & Verification Course offers hands-on training in RTL design, FPGA programming, ASIC verification, and industry-standard EDA tools. Designed by IIT Madras-certified experts, this course provides job-ready skills to help you land top VLSI roles in chip design, embedded systems, and semiconductor industries.
5) Electromagnetic Interference (EMI) and Electromagnetic Compatibility (EMC) Issues
Modern chips running at higher frequencies create stronger electromagnetic disturbances, which has made electromagnetic interference (EMI) a growing concern as semiconductor technology advances. These disturbances can affect circuit performance, reliability, and how integrated circuits work.
EMI shows up in different ways and affects VLSI designs through conducted and radiated interference. While conducted EMI moves through power lines and conductors, radiated EMI travels through space. Millions of internal transistors switch at the same time in advanced process nodes. This creates faster and stronger steep currents that lead to more electromagnetic emissions.
Higher operating frequencies make EMI management more challenging. The way electromagnetic events behave randomly can’t be ignored anymore, especially since digital equipment has reached new levels of complexity.
Ways to Overcome:
- Shielding and Grounding: Use metal shielding, proper grounding techniques, and optimized PCB layouts to reduce EMI.
- Design for Signal Integrity: Implement differential signaling, impedance matching, and controlled trace routing to minimize interference.
- Power Integrity Management: Employ decoupling capacitors, low-noise power delivery networks, and on-chip voltage regulators.
- Advanced Simulation and Testing: Use electromagnetic simulation tools and pre-compliance testing to detect and mitigate EMI early.
- Regulatory Compliance Standards: Adhere to industry standards (e.g., IEC, FCC, CISPR) to ensure EMC certification.
6) Manufacturability and Yield Optimization
Wafer processing costs depend heavily on production yield, which affects output efficiency and financial viability. The industry has seen some concerning trends lately. Intel had to push back its 7nm chip production by six months in 2020 because of yield problems. Samsung’s situation looks even more challenging – their yield rate on 4nm chips fell to 35%, while TSMC achieved 70%.
Advanced process nodes create unique obstacles for yield optimization. Each wafer goes through hundreds of precise processes that take three to six months to complete. Tiny contaminants can make a chip defective. This makes yield management trickier as features get smaller. Manufacturers must meet tough industry standards.
Critical area analysis makes yield optimization more complex by showing how sensitive designs are to random manufacturing defects. Engineers must carefully calculate defect size distributions and what they mean for circuit functionality. Modern tools and algorithms help designers spot and fix yield-limiting issues early in the design process.
Ways to Overcome:
- Design for Manufacturability (DFM): Implementing DFM techniques such as optical proximity correction (OPC) and layout-aware optimizations to enhance fabrication reliability.
- Process Variation Modeling: Using statistical analysis and machine learning to predict and mitigate the impact of manufacturing variations on chip performance.
- Redundancy and Error Correction: Employing built-in self-repair (BISR) and error correction mechanisms to improve functional yields.
- Advanced Yield Monitoring: Leveraging AI-driven defect detection and real-time monitoring to identify yield-limiting factors early in production.
- Collaboration with Foundries: Working closely with semiconductor foundries to refine process recipes and ensure design compatibility with manufacturing constraints.
7) Cost and Time-to-Market Pressures
Competition in the semiconductor industry requires shorter development cycles that don’t compromise quality. Product life cycles keep getting shorter, and VLSI designers must deliver high-quality designs quickly.
VLSI designers traditionally use manual exploration to find the right balance between performance metrics and fabrication costs. The design space has grown so big and complex that manual exploration no longer works well enough to find the best solutions. VLSI design costs include mask costs, wafer costs, packaging expenses, and testing expenditures.
These costs directly shape the product’s economic viability. Designers now use algorithm-driven searches to update parameters based on gradients and historical information. Good planning of prototyping processes and thorough design reviews reduce the number of needed prototypes, which cuts development costs.
Ways to Overcome:
- Adopting Design Automation Tools – Leveraging AI-driven Electronic Design Automation (EDA) tools for design synthesis, verification, and layout optimization accelerates the development process.
- Using Pre-Verified IP Blocks – Incorporating reusable, pre-verified Intellectual Property (IP) cores minimizes design time and reduces validation efforts.
- Parallel Processing & Cloud-Based Simulation – Utilizing high-performance computing (HPC) and cloud-based simulations enables faster verification and testing cycles.
- Early Design-for-Manufacturing (DFM) Considerations – Addressing manufacturability early in the design phase reduces costly re-spins and fabrication errors.
- Collaboration with Foundries – Close collaboration with semiconductor fabs ensures better yield predictions, process optimizations, and cost-effective manufacturing strategies.
8) Interdisciplinary Skills Requirement
VLSI design success requires mastery of multiple disciplines. Research shows 60% of design challenges come from overlapping technical domains. The field has grown beyond traditional electronic engineering, and professionals now need both technical expertise and people skills.
Front-end and back-end specialists need different skills. Digital logic design, Boolean algebra, and sequential circuits are the life-blood of VLSI success. Designers use this knowledge to analyze waveforms, spot timing violations, and fix problems quickly.
The field needs constant learning and adaptation to new technologies. Professionals must track industry trends, learn new design tools, and embrace modern methods. Real industry projects help build teamwork, decision-making, and cross-cultural management skills. Hence, constant learning and keeping up with trends has become a must.
Ways to Overcome:
- Cross-Disciplinary Training: Encourage VLSI engineers to upskill in related fields like AI, cryptography, and embedded systems through specialized courses.
- Collaborative Development: Promote interdisciplinary collaboration between hardware, software, and system engineers to enhance holistic problem-solving.
- Advanced EDA Tools Proficiency: Train designers to leverage AI-powered EDA (Electronic Design Automation) tools for efficient circuit optimization and verification.
- Industry-Academic Partnerships: Foster partnerships between universities and semiconductor companies to bridge gaps in interdisciplinary skill development.
- Open-Source Engagement: Participate in open-source VLSI and FPGA projects to gain hands-on experience with multi-domain integration.
Takeaways…
The semiconductor industry’s rapid progress shapes today’s VLSI design challenges. Modern chips need exceptional power efficiency, signal integrity, and manufacturing precision. Verification bottlenecks take up much time, but teams can overcome these hurdles with proper planning and advanced tools.
Yield optimization is vital to control costs, and EMI management will give a reliable chip operation. Success comes from becoming skilled at multiple disciplines while keeping up with new technologies. A deep grasp of these challenges helps you navigate complex VLSI projects well.
Moving ahead requires you to think over design complexity, power limits, and market timing pressure. This knowledge helps you tackle key challenges as you create economical, reliable semiconductor solutions that match industry needs.
FAQs
The key challenges include managing increasing design complexity, optimizing power consumption, ensuring signal integrity and timing closure, addressing electromagnetic interference issues, and improving manufacturability and yield. Designers also face pressure to reduce costs and time-to-market while requiring interdisciplinary skills.
Power management is a critical concern in VLSI design, especially for portable devices. Designers must balance performance with power efficiency, addressing both static and dynamic power dissipation. Techniques like multi-threshold voltage design, power gating, and dynamic voltage scaling are employed to optimize power consumption.
Verification is crucial in ensuring design correctness and functionality. It involves simulation techniques, functional verification, and assertion-based methodologies. As designs grow more complex, verification becomes increasingly challenging, often consuming a significant portion of the design cycle time.
Manufacturing challenges significantly impact VLSI design, particularly at advanced process nodes. Designers must consider issues like deep sub-wavelength lithography complications, random defect occurrences, and chemical-mechanical polishing issues. Yield optimization requires both correct-by-construction and construct-by-correction approaches.
VLSI designers need a diverse skill set including expertise in digital logic design, mixed-signal design, verification methodologies, and physical design. Strong analytical thinking, problem-solving abilities, and communication skills are crucial. Continuous learning is essential to keep up with emerging technologies and industry trends.
Did you enjoy this article?