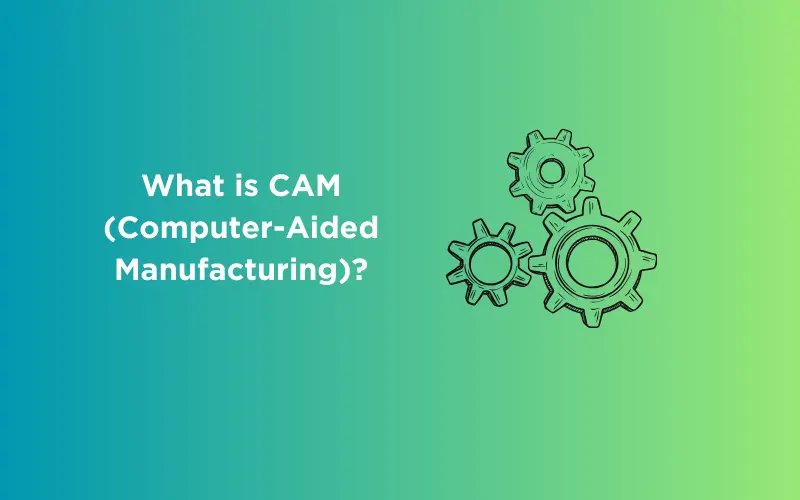
What is CAM (Computer-Aided Manufacturing)?
Jul 01, 2025 5 Min Read 6324 Views
(Last Updated)
CAM (Computer-Aided Manufacturing) is a computer software and machinery to automate and optimize the manufacturing process. It bridges the gap between digital design (CAD) and physical production, enhancing precision, efficiency, and adaptability, especially in aerospace, automotive, and medical manufacturing industries.
In the evolving landscape of manufacturing, a digital revolution is shaping the way we bring ideas to life. CAM is a technological marvel that seamlessly fuses the precision of computer-aided design (CAD) with the tangible realities of the production floor.
What sets CAM apart, and how does it revolutionize traditional production methods? In this comprehensive blog, join us as we uncover the indispensable role of CAM in shaping the future of the manufacturing field. Let’s quickly demystify CAM while understanding its advantages and disadvantages, exploring its expansive scope, and witnessing its real-world applications across various growing industries.
Table of contents
- What is CAM (Computer-Aided Manufacturing)?
- CAM Vs CAD
- CAM Workflow
- Digital Design using CAD
- Importing the Design into CAM Software
- Toolpath Generation
- Machine Setup
- Material Preparation
- Manufacturing Process
- Quality Control and Inspection
- Final Product
- Advantages of CAM
- Precision and Accuracy
- Increased Production Speed
- Reuse of Design Data
- Enhanced Efficiency
- Cost Reduction
- Adaptability
- Disadvantages of CAM
- Very High Implementation Cost
- Risk of Over-Reliance on Automation
- Cybersecurity Concerns
- Why You Should Learn CAM?
- High Scope
- Enhanced Career Opportunities
- Increased Productivity and Efficiency
- Competitive Advantage
- Versatility Across Industries
- Collaboration with CAD Professionals
- Job Security and Future-Proofing
- Wrapping Up
- FAQs
- What is the difference between CAD and CAM?
- What are the uses of CAM?
- Can CAM be applied to small-scale manufacturing?
- Why do mechanical engineers use CAD?
What is CAM (Computer-Aided Manufacturing)?
Computer-Aided Manufacturing (CAM) is the use of computer software and machinery to automate and facilitate the manufacturing process smartly. It acts as the bridge between conceptualization and creation, optimizing efficiency and precision in the production pipeline. CAM is an effective software that interprets CAD models and translates them into instructions for machines, ensuring the precise and efficient fabrication of components and products.
Before we move on to the next part, you should have a deeper knowledge of key mechanical engineering concepts. You can consider enrolling in GUVI’s CAD Course for Mechanical Engineers, which lets you gain practical experience by developing real-world projects and covers technologies including AutoCAD, Solidworks, CATIA, Ansys, GD&T, etc.
Additionally, if you would like to explore AutoCAD for Mechanical Engineering through a self-paced course, you can take GUVI’s AutoCAD Mechanical Certification Course.
CAM Vs CAD
- CAD (Computer Aided Designing) focuses on creating detailed digital models and designs, while CAM (Computer Aided Manufacturing) brings those design ideas and digital models to life.
- CAD offers a virtual blueprint for products by envisioning and conceptualizing ideas. CAM, on the other hand, is the realization stage, where the digital design is meticulously translated into instructions that machines follow to manufacture the actual product.
CAM Workflow
The CAM workflow outlines the series of steps involved in using computer software and machinery to automate the manufacturing process. It plays a crucial role in transforming digital designs into tangible products. Here’s an overview of the typical CAM workflow:
Digital Design using CAD
- The process begins with the creation of a digital design using Computer-Aided Design (CAD) software.
- This digital model serves as a virtual blueprint for the desired product, encompassing detailed specifications and dimensions.
Explore Generating Concepts for Product Design: Step-by-Step Guide [2025]
Importing the Design into CAM Software
- Once the CAD design is complete, it is imported into CAM software.
- CAM software interprets the digital design and translates it into machine-readable instructions for manufacturing.
Toolpath Generation
- Toolpaths are the precise routes that cutting tools or machinery will follow to shape and form the raw materials into the final product.
- CAM software analyzes the digital design and generates toolpaths.
- This step is crucial for ensuring accuracy and efficiency in the manufacturing process.
Machine Setup
- Based on the generated toolpaths, the manufacturing machinery is set up and calibrated.
- This involves configuring the tools, materials, and other parameters to match the requirements of the specific manufacturing project.
Material Preparation
- Raw materials, such as metal, plastic, or wood, are prepared for the manufacturing process.
- This may involve cutting, shaping, or treating the materials based on the design requirements.
Manufacturing Process
- The CAM system guides the machinery through the manufacturing process.
- This can include cutting, milling, turning, or other operations, depending on the design specifications.
- The machinery follows the pre-determined toolpath to shape the raw materials into the final product.
Quality Control and Inspection
- After the manufacturing process, the finished product undergoes quality control and inspection.
- This ensures that it meets the required standards and specifications outlined in the initial CAD design.
Final Product
- The result is a tangible product that mirrors the digital design with high precision.
- The CAM workflow ensures consistency and accuracy in the manufacturing process, minimizing errors and maximizing efficiency.
Advantages of CAM
CAM offers infinite advantages that significantly impact the efficiency, precision, and overall effectiveness of the manufacturing process. Here are some key advantages of CAM:
1. Precision and Accuracy
CAM has exceptional precision and accuracy in its manufacturing process. Unlike manual operations, CAM systems execute tasks with minimal deviation, ensuring that each product adheres to the exact specifications outlined in the digital design.
2. Increased Production Speed
One of the primary advantages of CAM is Automation which leads to increased production speed. CAM systems optimize the manufacturing process, enabling faster cycles and allowing businesses to meet demands and deadlines more effectively. This acceleration is particularly beneficial in industries with high production volumes.
3. Reuse of Design Data
CAM helps you reuse design data. This action minimizes redundancy in the manufacturing process. Once a design is created, it can be stored and utilized for future production. This not only saves time but also makes the process sustainable by reducing the need for repetitive design work.
4. Enhanced Efficiency
CAM systems automate complex tasks without manual intervention in many stages of production. This not only reduces the likelihood of errors but also enhances overall efficiency by streamlining processes. CAM’s ability to optimize toolpaths and manufacturing processes contributes to a more efficient use of available resources.
5. Cost Reduction
Despite the initial investment required for CAM implementation, the long-term benefits often translate into cost reductions. The automation of tasks reduces labor costs, minimizes material wastage, and lowers the likelihood of errors that could lead to costly rework. Additionally, the reuse of design data contributes to time and resource savings.
6. Adaptability
CAM allows quick adaptation in industries where design changes are frequent. Adjustments to the digital design can be seamlessly integrated into the manufacturing process, reducing downtime and accelerating the overall product development cycle.
Also Read | Generative Design: Navigating the Future of Mechanical Engineering
Disadvantages of CAM
While CAM offers a ton of advantages, it is also important to consider its potential disadvantages and challenges associated with its implementation. Here are some key disadvantages of CAM:
1. Very High Implementation Cost
The integration of CAM systems involves a significant initial investment. This cost includes the acquisition of CAM software, its specialized machinery, and the training of employees to operate these systems. The upfront costs can be a major obstacle for certain small to medium-sized businesses.
2. Risk of Over-Reliance on Automation
While automation brings efficiency, there is a potential risk of over-reliance on it. Depending too heavily on automated processes may limit adaptability to unforeseen changes in the production environment. Striking the right balance between automation and manual intervention is essential.
3. Cybersecurity Concerns
The integration of digital technology in manufacturing processes brings about cybersecurity concerns. CAM systems, connected to networks for data transfer and updates, may be vulnerable to cyber threats. Ensuring robust cybersecurity measures is crucial to protect sensitive manufacturing data.
Why You Should Learn CAM?
Learning Computer-Aided Manufacturing (CAM) is a valuable investment for mechanical engineering and manufacturing aspirants seeking to thrive in modern manufacturing environments. Here are compelling reasons why learning CAM can be beneficial:
1. High Scope
CAM skills are in high demand across various industries, including aerospace, automotive, medical, and electronics. Acquiring proficiency in CAM positions you as a valuable asset to employers seeking individuals with expertise in digital manufacturing processes.
2. Enhanced Career Opportunities
As industries increasingly embrace automation and digitalization, professionals with CAM skills are highly-demanded and offered a lot of career opportunities. Proficiency in CAM opens doors to diverse roles within the industries like manufacturing, design, or engineering.
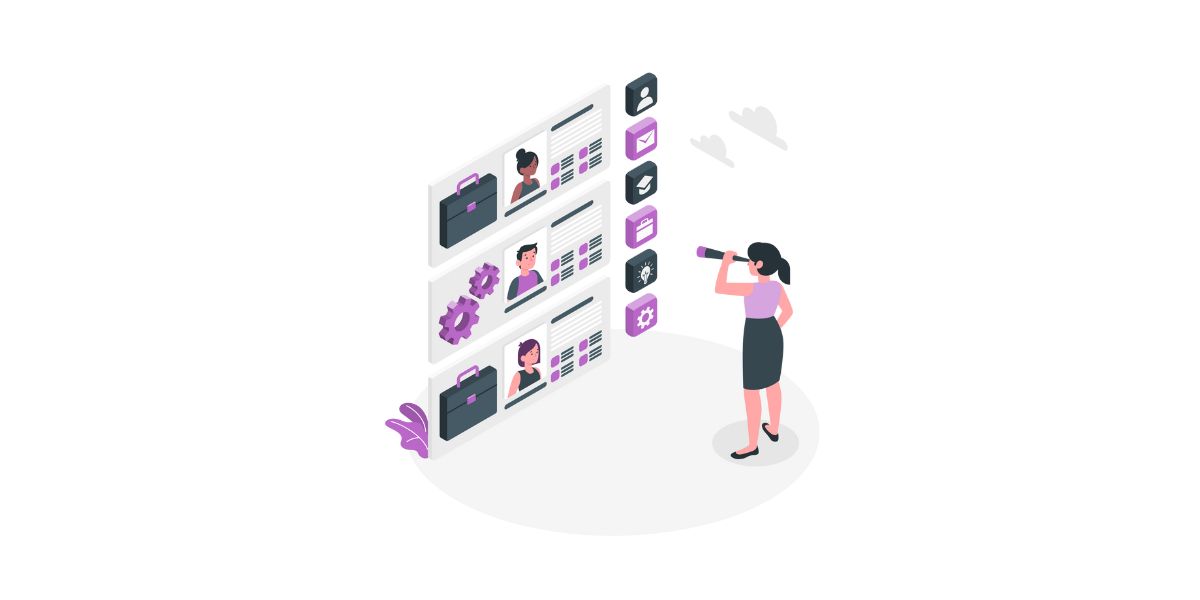
3. Increased Productivity and Efficiency
CAM automates and optimizes manufacturing processes, leading to increased productivity and efficiency. By learning CAM, you empower yourself to contribute to streamlined production workflows, reduced lead times, and enhanced overall operational efficiency.
4. Competitive Advantage
In a competitive job market, acquiring CAM skills gives you a competitive edge. Employers are often on the lookout for candidates who not only understand traditional manufacturing processes but are also proficient in digital technologies to optimize production.
5. Versatility Across Industries
CAM skills are versatile and applicable across a wide range of industries. The principles of CAM remain relevant in industries like aerospace, automotive, medical device manufacturing, and electronics. This allows you to explore various sectors and diversify your career options.
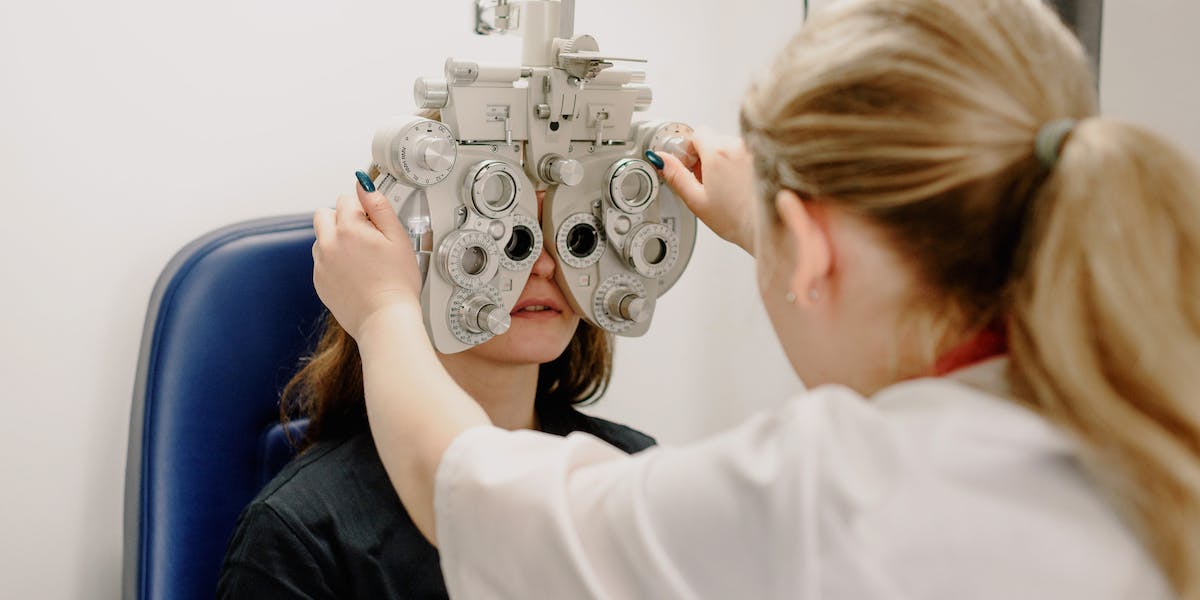
6. Collaboration with CAD Professionals
CAM often goes hand in hand with Computer-Aided Design (CAD). Learning CAM enables you to collaborate effectively with CAD professionals, bridging the gap between design and production. This collaborative skill set is highly valued in integrated manufacturing environments.
7. Job Security and Future-Proofing
Industries are increasingly investing in automation and digital technologies. Learning CAM positions you as a professional with skills aligned with the future of manufacturing, providing job security and future-proofing your career against evolving industry demands.
Find out more Promising Scope of Mechanical Engineering in India in 2025
Kickstart your career by enrolling in GUVI’s CAD Course for Mechanical Engineers, where you will master technologies including AutoCAD, Solidworks, CATIA, Ansys, GD & T, etc, and build interesting real-life mechanical projects.
Alternatively, if you would like to explore AutoCAD for Mechanical Engineering through a self-paced course, you can take GUVI’s AutoCAD Mechanical Certification Course.
Wrapping Up
Computer-aided manufacturing (CAM) has emerged as a transformative force in the world of industrial production. As we explored CAM, we’ve witnessed a convergence of design and technology that reshapes the way we conceptualize and create. The scope of CAM knows no bounds, reaching into diverse industries and leaving a memorable mark on the future of manufacturing.
Also, remember that learning CAM is not just about acquiring a specific skill set. It’s a strategic move toward building a dynamic and future-ready career. The synergy between CAM and CAD paves the way for innovation and progress. So, get started with GUVI’s CAD course, exclusively designed for Mechanical Engineers.
FAQs
CAD (Computer-Aided Design) focuses on creating digital models and designs based on design concepts. CAM (Computer-Aided Manufacturing) is concerned with realizing the concepts with automated production processes based on CAD designs.
CAM is used in aerospace, automotive, medical, and electronics industries in their respective product manufacturing processes.
Yes, CAM can be adapted for small-scale manufacturing. The level and cost of implementation may vary, but even in smaller setups, CAM can enhance precision and efficiency in the production process.
Mechanical engineers use AutoCAD computer software to create digital models of mechanical parts, components, and systems.
Did you enjoy this article?